单绞机差速器,电缆制造领域的核心技术突破
发布日期:2025-02-25 浏览次数:285
前言
在电线电缆制造行业中,设备的高效性与稳定性直接决定了产品质量与生产成本。随着5G通信、新能源汽车等领域的快速发展,市场对高性能线缆的需求呈现指数级增长。而在这背后,一项名为单绞机差速器的技术正悄然成为行业升级的“隐形推手”。它不仅解决了传统绞合工艺中的效率瓶颈,更通过精密的速度调控实现了线缆结构的革命性优化。本文将深入解析这一技术的核心原理、应用场景及其对产业升级的深远影响。
一、单绞机差速器的核心功能与结构设计
单绞机是电线电缆生产中的关键设备,其核心任务是将多根金属导体或绝缘线芯按特定规则绞合成缆。而差速器的作用,则是通过调节绞合过程中不同部件的转速差,确保线芯张力均匀、绞合节距精准。
1. 传统绞合工艺的痛点
在未引入差速控制技术前,单绞机的转速通常采用固定比例驱动。这种模式下,线芯易因张力波动出现“跳股”或“松紧不均”现象,导致产品合格率下降。此外,设备在高速运转时,机械磨损加剧,维护成本显著增加。
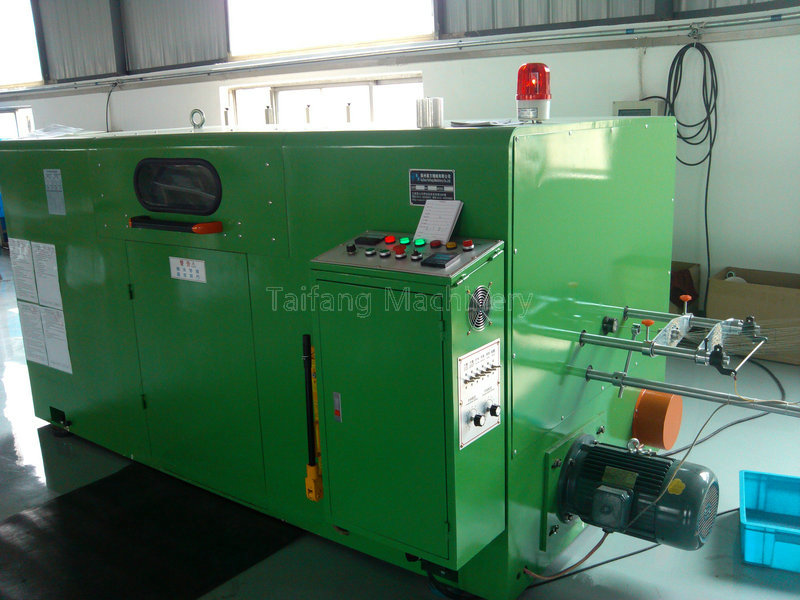
2. 差速器的革新设计
现代单绞机差速器采用模块化传动系统,通过伺服电机、编码器与PLC控制单元的协同工作,动态调整放线盘、绞合转笼、收线装置的转速差。例如,在绞合直径变化时,系统可实时计算并补偿线芯长度差异,确保张力恒定。这种设计使绞合速度提升30%以上,同时将废品率控制在0.5%以内。
二、差速调节技术的三大核心突破
1. 闭环反馈控制系统
通过高精度编码器实时监测线芯张力与转速,PLC将数据与预设参数对比后,立即调整伺服电机的输出扭矩。这一闭环控制模式打破了传统开环系统的滞后性,尤其适用于超细导体(如直径0.03mm漆包线)的精密绞合。
2. 动态补偿算法
在绞合不同截面线缆时,差速器内置的算法可预测因转笼惯性导致的转速偏差,并提前进行补偿。例如,某品牌设备通过动态惯性补偿(DIC)技术,将换向时的速度波动从±5%降至±0.8%,显著提升了绞合节距的一致性。
3. 多轴协同驱动架构
新一代差速器采用多轴独立驱动设计,每个放线单元均配备独立伺服电机。这种架构不仅简化了机械传动链(减少齿轮箱依赖),还支持非对称绞合(如7+1结构)等复杂工艺,为特种电缆制造提供了可能。
三、应用场景与经济效益分析
1. 通信电缆领域
在5G基站用漏泄电缆的生产中,差速器通过精确控制铜带与绝缘层的绞合速度,使信号衰减值降低15%。某头部企业采用该技术后,单条产线年产能突破10万公里,较传统设备提升42%。
2. 新能源汽车线束制造
高压线束对绞合均匀性要求极高。通过差速器的主动阻尼调节功能,可在800m/min高速绞合下,确保每根导体的延伸率误差≤0.2%。这一突破使特斯拉等车企的线束采购成本下降18%。
3. 航空航天特种线缆
针对耐高温、抗辐射线缆的制造需求,差速器通过低温升驱动方案(采用陶瓷轴承与油冷电机),将设备连续工作温度控制在45℃以下,避免了材料热老化导致的性能劣化。
四、未来趋势:智能化与绿色化融合
随着工业4.0的推进,单绞机差速器正朝着两个方向演进:
- 高精度传感器的成本压力:纳米级编码器的价格约占设备总成本的15%。部分厂商正通过国产化替代(如采用磁栅传感器)将成本压缩至原有水平的60%。
- 复合型人才短缺:同时精通机械传动与控制算法的工程师全球缺口超过2万名。头部企业已与高校合作开设“智能装备控制”微专业,定向培养跨学科人才。
—
通过上述分析可见,单绞机差速器已从单纯的机械部件进化为融合传感、算法、材料的系统工程。其技术突破不仅推动了线缆制造业的升级,更为半导体封装、医疗器械等关联领域提供了跨界创新灵感。在“双碳”目标与数字化转型的双重驱动下,这一技术的潜力远未触顶。
TAG: