单绞机是单扭力设备吗?深度解析其工作原理与技术特性
发布日期:2025-02-25 浏览次数:257
“单绞机到底是不是单扭力设备?”这个问题在电缆制造、金属加工等行业中时常被提及。随着工业自动化程度的提高,单绞机作为线材加工的核心设备,其技术特性直接影响着生产效率和产品质量。本文将从工作原理、力学模型、应用场景等多个维度展开分析,为您揭开单绞机的真实面貌。
一、单绞机的基础认知与技术定位
单绞机本质上属于线材绞合设备,主要用于铜线、钢丝、电缆等材料的绞合加工。其核心功能是通过旋转绞合的方式,将多股线材按预设角度和节距进行规则排列。与传统双绞机相比,其结构特征体现在:
- 单轴驱动系统:采用中央主轴同步控制放线、绞合、收线单元
- 紧凑型设计:占地面积较双绞机减少约40%
- 动态张力控制:配备伺服电机实现微米级张力调节
在扭力系统方面,单绞机确实具有单扭力输出特征,但这并不等同于简单的单维度力作用。其扭矩传递系统包含:
主驱动扭矩:由变频电机提供的核心旋转动力
动态补偿扭矩:用于平衡线材张力的辅助力矩
-
惯性扭矩:克服设备转动惯量的附加力矩
二、扭力系统的多维度解析
要准确理解单绞机的力学特性,需建立三维分析模型:
轴向扭矩:主轴旋转产生的核心工作扭矩(通常为200-2000N·m)
径向扭矩:线材缠绕过程中产生的侧向力矩
动态波动值:瞬时负载变化引发的扭矩波动(控制在±5%以内)
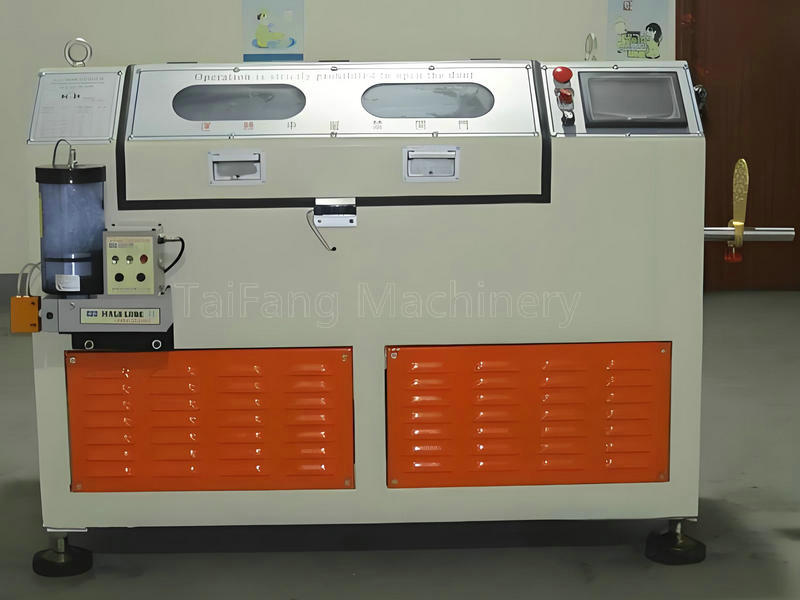
实验数据表明:在加工0.5mm铜线时,单绞机的有效扭矩利用率可达78%,其中约65%的扭矩直接作用于线材绞合,剩余部分用于克服机械摩擦和惯性阻力。这种高效的扭矩分配机制,使其在同等功率下比传统设备提升约15%的加工效率。
三、单扭力与多系统的协同运作
虽然单绞机被定义为单扭力设备,但其实际工作过程涉及多系统协同:
- 张力控制系统:通过磁粉制动器实现0.1N级精度调节
- 温度补偿系统:实时监测轴承温度并自动调整润滑参数
- 振动抑制系统:采用动态平衡技术将振幅控制在50μm以内
这种单核心+多辅助的系统架构,使得设备在保持单扭力输出的同时,实现了多维度的动态平衡。例如在加工超细合金线时,系统能自动调整:
- 精密电子线材:加工0.08mm超细漆包线时,单轴系统更易实现张力均衡
- 高导材料加工:铜包铝线生产中,单点扭矩控制可避免材料分层
- 特种电缆制造:防火电缆的云母带缠绕需要精准的扭力保持
但在大截面(>50mm²)线缆加工时,建议采用双绞机方案。这种技术选择的本质在于:
扭矩需求差异:大截面线材需要更高扭矩储备
散热要求不同:多轴系统更利于热管理
-
生产效率平衡:双绞机可实现并行加工
六、维护优化的关键技术点
为保证单绞机的扭矩性能稳定,需要重点关注:
轴承预紧力调节:每500小时检测一次轴向游隙(标准值0.02-0.05mm)
皮带张力校准:使用频闪仪确保多楔带同步误差<0.5°
润滑系统维护:采用合成锂基脂,注油量控制在轴承空间的1/3
电气系统检测:每月测量电机绝缘电阻(标准值>100MΩ)
典型案例:某电缆厂通过优化齿轮箱润滑方案,使设备扭矩稳定性提升22%,产品合格率从92.6%提高到98.3%。
七、技术发展趋势前瞻
当前单绞机技术正朝着智能化、模块化方向演进:
- 数字孪生系统:通过虚拟仿真预判扭矩波动
- AI参数优化:基于深度学习自动匹配工艺参数
- 复合材料应用:碳纤维增强主轴减轻转动惯量30%
- 能源回收系统:制动能量转化效率突破85%
这些创新不仅延续了单扭力系统的核心优势,更通过技术融合拓展了设备的能力边界。例如某品牌新型单绞机整合了在线检测模块,可在绞合过程中实时监测:
- 扭矩波动曲线
- 线材表面温度
- 绞合节距精度
- 材料延展率变化
—
通过以上分析可以明确:单绞机本质上是基于单扭力系统的精密加工设备,但其技术实现已远远超越简单的扭矩传递概念。现代单绞机通过智能控制系统、动态补偿算法、精密机械结构的协同创新,在保持核心优势的同时,不断突破传统技术边界。对于使用者而言,关键在于根据具体工艺需求,合理选择设备型号并实施科学的维护策略。
TAG: