收线机排线器调整指南,精准控制线材收卷的5个关键步骤
发布日期:2025-03-07 浏览次数:393
在金属加工、线缆制造等行业中,收线机排线器的运行状态直接影响线材收卷的平整度与生产效率。一台未正确校准的排线器,轻则导致线盘边缘磨损,重则引发断线、叠线事故。如何科学调整排线器参数,使其适应不同线径与收卷速度?本文将拆解操作流程,提供一套可落地的调试方案。
一、排线器调整前的准备工作
调整排线器前需明确设备型号、线材特性、收卷工艺要求三大要素。例如:处理0.5mm铜线与5mm钢缆时,排线器的往复速度、张力补偿值差异显著。建议先查阅设备说明书,确认排线器的行程范围、最大线径兼容值等参数。
关键工具准备:
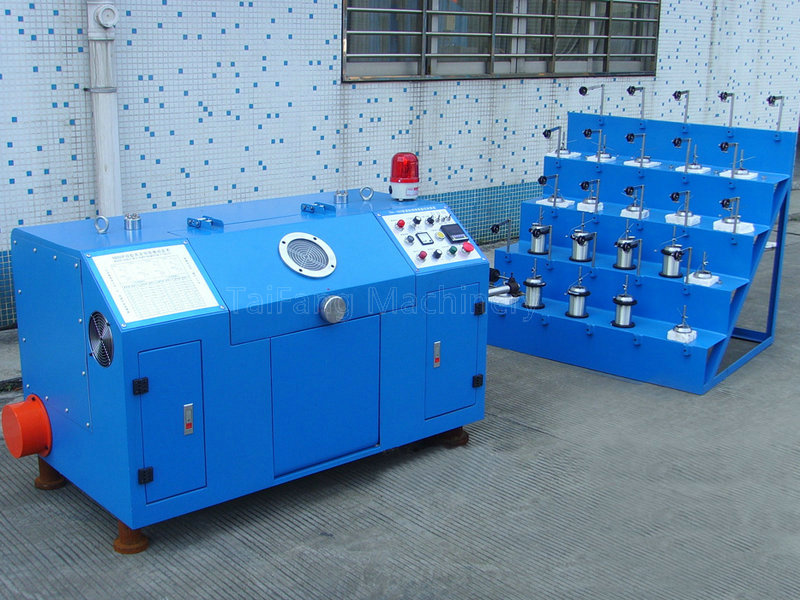
- 千分尺(测量线材实际直径)
- 激光测距仪(检测排线器横向移动精度)
- 张力计(验证线材收卷张力是否均匀)
二、校准排线器的“零点基准”
排线器的初始位置偏差是导致收卷偏移的常见原因。操作步骤如下:
- 关闭设备电源,手动旋转排线丝杆,使排线导轮移动至机械原点(通常标记为刻度“0”位置);
- 松开排线器支架的固定螺栓,用水平仪调整导轨与收线盘的平行度(误差需≤0.1mm/m);
- 重新启动设备,通过控制面板的“归零”功能同步电子编码器与机械位置。
注意:部分型号设备需在归零后执行行程自检程序,避免排线器撞限位开关。
三、调节排线器的往复速度与换向点
排线速度需与主轴收卷转速匹配。过快会导致线材堆积,过慢则形成间隙。计算公式为:
排线速度(m/min)= 主轴转速(r/min)× 线材直径(mm) × π ÷ 1000
实际操作中:
- 在触摸屏输入线径实测值,系统自动计算理论排线速度;
- 通过增量调节法微调:启动设备后观察3-5个往复周期,若线材出现间隙,将速度提高5%-10%;若重叠,则降低速度;
- 换向点调整需确保排线导轮在距离线盘边缘2-3mm处反向,防止“塌边”现象。
四、优化排线张力补偿参数
张力不均会导致线材松紧不一,影响后续放线工序。调整要点包括:
- 预紧力设置:通过气压阀或磁粉制动器,使线材在静止状态下保持轻微张力(建议值为工作张力的30%);
- 动态补偿:在排线换向瞬间,系统需自动增加10%-15%的张力,抵消惯性导致的松线风险;
- 异常报警阈值:设定张力波动超过±20%时触发停机保护。
五、动态调试与验证
完成参数设定后,需进行空载测试与负载测试:
- 空载测试:断开收线电机,观察排线器往复运动是否平滑,换向时有无异响;
- 负载测试:使用废线进行低速(30%额定速度)收卷,检查线层是否紧密、无交叉;
- 高速验证:逐步提升至满速,监测张力曲线与排线位置反馈信号是否稳定。
典型问题解决方案:
- 叠线问题:检查主轴编码器信号是否丢失,或排线器丝杆导程参数输入错误;
- 边缘毛刺:调整换向点缓冲参数,减少机械冲击;
- 周期性波动:清洁排线导轨并涂抹特种润滑脂(如氟素脂),消除阻力不均。
维护建议:延长排线器寿命的3个细节
- 每月清理排线导轮沟槽内的线材碎屑,避免卡滞;
- 每季度检查丝杆与直线导轨的磨损量,超过0.2mm需更换;
- 采用红外热像仪定期监测驱动电机温升,异常发热往往预示轴承故障。
TAG: